基于有限元的钻杆螺纹失效分析案例
2022-12-2 10:31:32
详细介绍
煤矿用坑道钻机由于它重量轻,能解体,操作简单,使用可靠,在煤矿已被广泛使用。在井下施工瓦斯抽放孔、注浆灭火孔、煤层注水孔、地质勘探孔及其它工程钻孔时,经常出现钻杆接头断裂事故。钻杆断裂不仅影响正常生产,而且还往往因难于打捞而使事故恶化,造成人力、财力的损失。从形式上看,由于连接螺纹应力集中的影响以及交变应力的作用,绝大多数都是在钻杆接头螺纹处发生断裂。因此,有必要对钻杆的接头进行研究,以寻求和探讨解决的途径。根据现场考察发现,目前使用的 Φ42 钻杆存在以下失效形式:
钻进过程中,钻杆是通过螺纹连接而成的细长管柱,在钻头引导下进入已钻孔底部进行钻进,钻杆内外环中有钻孔液流动,钻杆与孔壁之间有环型间隙存在。钻杆的受力变形由两部分组成,第一部分是已钻孔形态迫使直线钻杆产生弯曲变形。第二部分是钻杆在钻进过程中产生的组合变形,一方面钻头处的轴向集中力(钻压),而钻压又受钻杆变形影响,属几何非线性动力学问题;另一方面,钻杆在各种载荷的作用下,其变形受到孔眼约束,与孔壁在任一深度位置、任一孔壁圆周方向上产生接触,属接触非线性动力学问题。
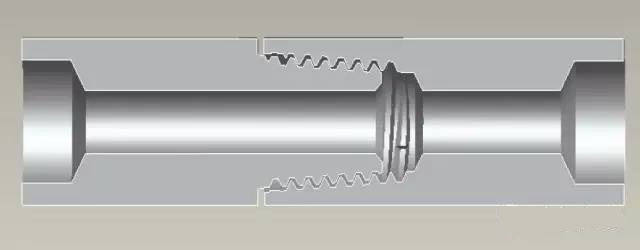
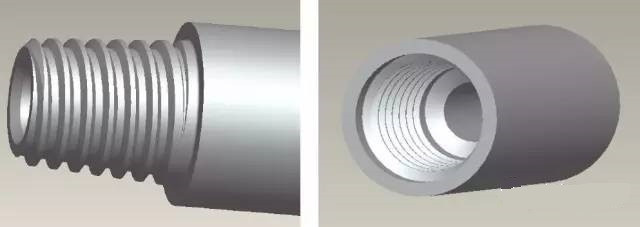
钻杆接头结构设计采用 2D 轴对称单元模拟,轴对称单元能以较小的计算成本达到非常高的精度。这里采用轴对称单元进行二维有限元分析计算。
利用 ABAQUS 软件对所建立的有限元模型进行计算,得出在该受力工况下的应力图,如图 4~6 所示:
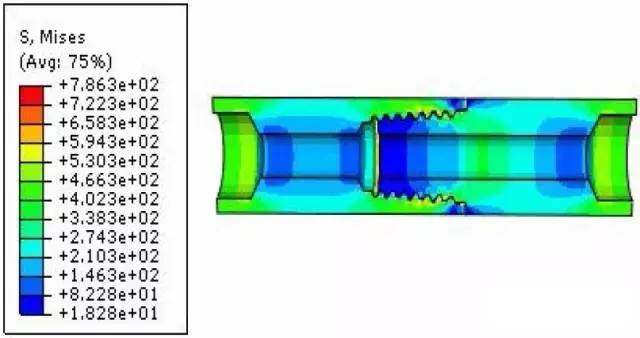
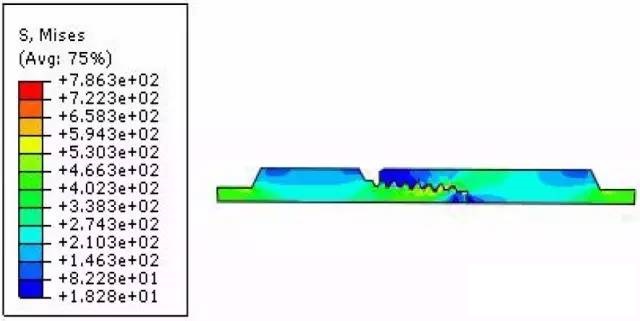
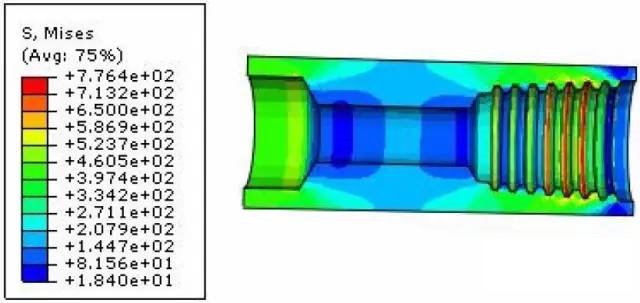
从图可以看出其最大等效应力为 786.3MPa,分布在公、母螺纹的第一牙处。,就钻杆接头部分强度分析计算而言,钻杆接头螺纹处(第一螺纹处)应力值偏大。如果钻杆选用 45号钢,钻杆接头螺纹强度明显不足;如果钻杆选用 40Cr,钻杆接头螺纹强度基本持平;如果钻杆选用 42CrMo,钻杆接头螺纹强度富余量也不明显。
根据上述分析可以看出,钻杆接头螺纹应力值偏高,接头螺纹强度偏低,是导致钻杆接头断裂的原因之一。
4钻杆材质分析
钻杆的断裂现象始终是与材料和结构的孔洞、缺口或裂纹相联系的。在材料的这种宏观不连续部分最明显的特点是应力分布不均匀,这种现象称为应力集中。缺陷(孔洞、缺口、裂纹等)和应力集中往往是造成结构破损的最重要原因。从抽象的观点讲,缺陷的出现,导致完整材料的某些对称性破缺,而且导致数学上的奇异性发生,值得一提的是,出现在钻杆上的裂纹通常是横向分布的,并且靠近“加厚过度带”早期出现的裂纹大都在锥型体与管柱之间过度区域的圆周上,这个过渡区强度很高,这些裂纹通常直而无分支,自然形成穿晶现象,而且这些现象总是伴随着疲劳断裂。
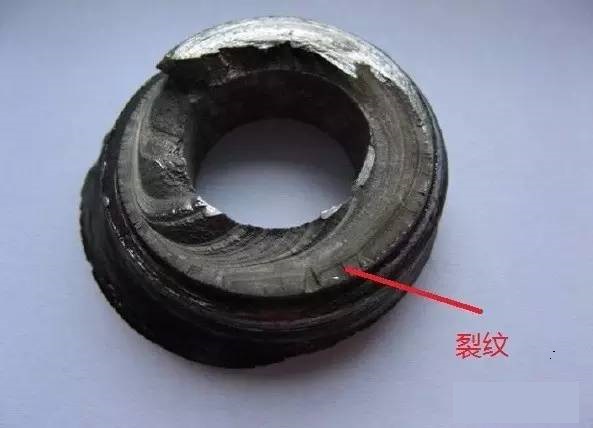
宏观形貌:肉眼观察发现,三次断口均有显著的旋转疲劳特征,第三次样件尤为明显。可见,裂纹起源于左上部位,在旋转载荷下沿逆时针方向疲劳扩展,断裂面积达到大约一半时(图 7 中直线处),弯曲应力的作用开始占据主导作用,疲劳纹大致与钻杆圆周平行。
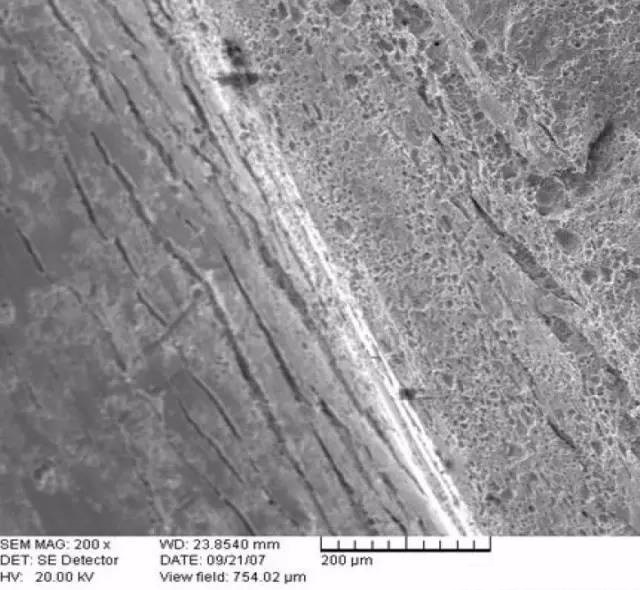

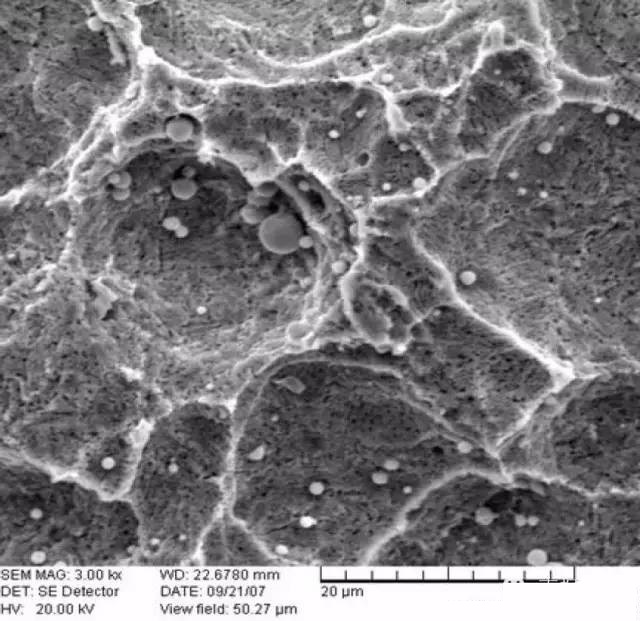
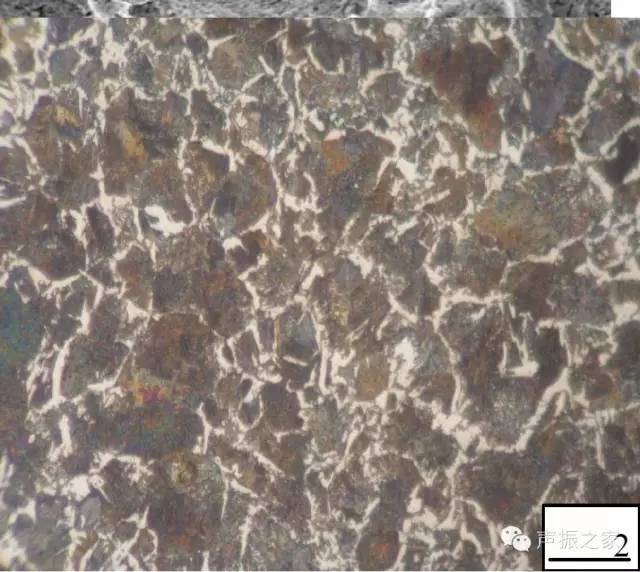
微观形貌:利用扫描电镜观察了断口的微观形貌。发现断口靠螺纹根部的边缘较为平坦,与此处的应力集中有关,螺纹面有大量腐蚀坑和小裂纹,说明腐蚀对裂纹的产生有一定促进作用;断口微观形貌以韧窝为主,显示韧性断裂特征;珠光体较多,是其硬度较高的原因之一。
5失效原因分析及改进措施
5.1 失效原因分析
通过对钻杆螺纹进行强度分析和材质分析,找出钻杆螺纹失效原因:
① 应力集中:钻杆接头螺纹原始模型有限元分析结果表明:在公扣第一螺纹牙处根部受到严重的应力集中,极容易引起疲劳破坏。
② 热处理工艺不稳定:通过钻杆的材质分析可以知道:钻杆过渡段形成一个组织不稳定的高应力区。如果在组织不稳定区的表面存在缺陷,它可能来自热处理中裂纹,也可能喷砂不均匀,成为疲劳源区。由于高应力的作用,接着在外部循环载荷的作用下,裂纹疲劳扩展,钻杆发生过载断裂。
③ 存在腐蚀:从分析的样品看,外表面发生了严重的腐蚀点坑,当蚀坑的深度使管子的壁厚承受不了内部压力时,穿孔现象就会发生。钻杆的腐蚀属于煤矿井下酸性环境引起的腐蚀。与断裂不同,腐蚀是一个缓慢的过程,蚀坑必然存在一个积累过程。防止腐蚀失效的措施,首先是钻杆存放位置尽量远离井下酸性环境的来源,其次是定期的清洗是可以避免腐蚀失效的。
5.2 改进措施
1) 结构改进措施:针对导致钻头断裂的原因,考虑改进方案与原设计的互换性问题,从以下两个方面进行改进:
切削公螺纹大端第一牙,使螺牙承受载荷均匀化;
开弯曲应力减荷槽,避免弯曲应力出现在螺纹薄弱区域;
改进前后结构对比见图12,按照上述方法重新对钻杆接头的强度进行有限元分析计算,计算结果见图13-15。
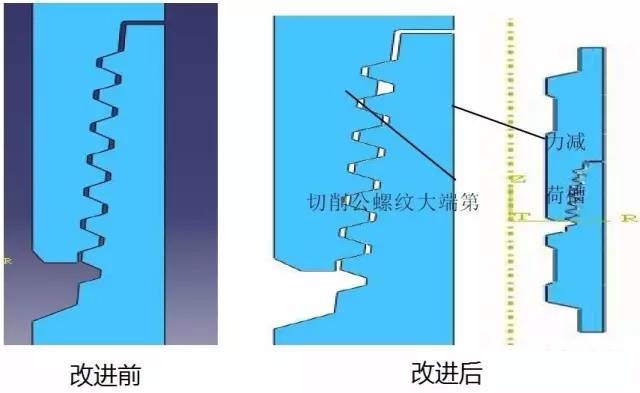
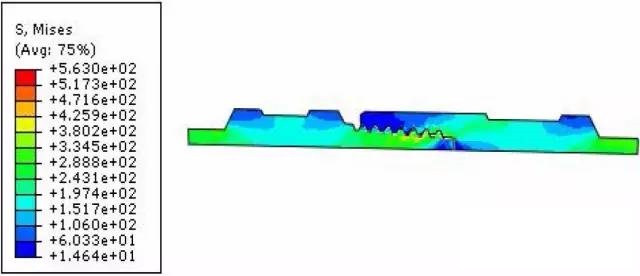
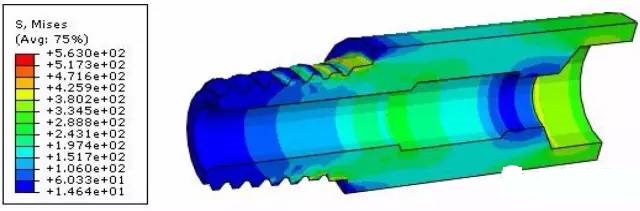
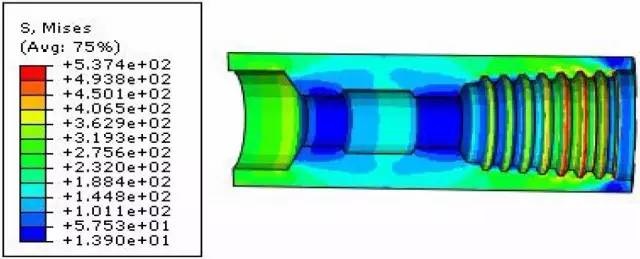
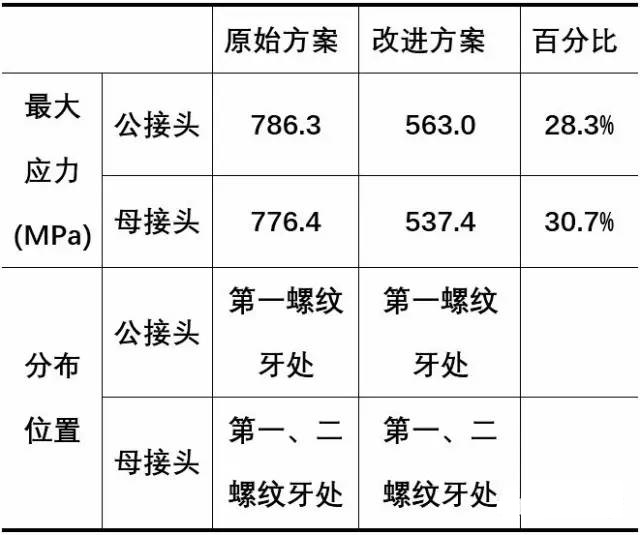
2) 材质及热处理改进措施:钻杆材料尽量选用强度较高的合金结构钢。严格控制热处理工艺和适当提高热处理后的硬度和强度,保证钻杆产品组织性能的均匀性和一致性。
6结论
通过上述改进措施加工出的钻杆,在全国多家大煤矿井下的实际应用,钻杆断裂的事故率明显降低,取得了较好的效果,为企业节约了大量的改进费用,缩短了改进时间,创造了较大的经济效益和社会效益。
Φ42 钻杆:公扣接头螺纹第 1~2 圈处断裂现象严重;母扣接头岔口现象严重;公、母扣磨损现象严重;少量钻杆弯曲现象;极少量接头与钻杆焊接部分断裂。
图1 钻杆断裂的实物图
2钻杆受力状况及实体模型钻进过程中,钻杆是通过螺纹连接而成的细长管柱,在钻头引导下进入已钻孔底部进行钻进,钻杆内外环中有钻孔液流动,钻杆与孔壁之间有环型间隙存在。钻杆的受力变形由两部分组成,第一部分是已钻孔形态迫使直线钻杆产生弯曲变形。第二部分是钻杆在钻进过程中产生的组合变形,一方面钻头处的轴向集中力(钻压),而钻压又受钻杆变形影响,属几何非线性动力学问题;另一方面,钻杆在各种载荷的作用下,其变形受到孔眼约束,与孔壁在任一深度位置、任一孔壁圆周方向上产生接触,属接触非线性动力学问题。
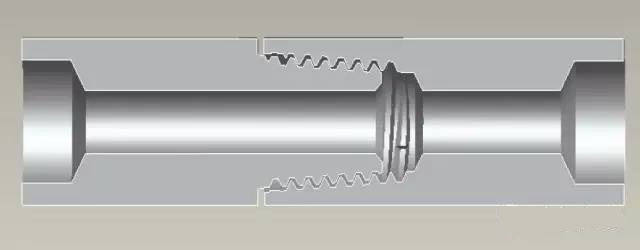
图2 钻杆接头几何模型
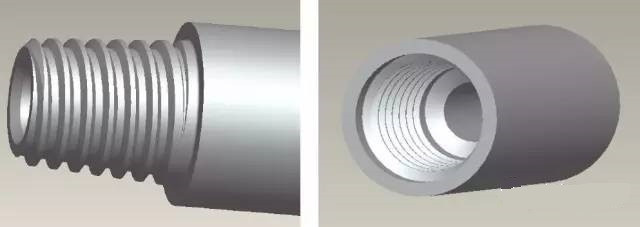
图3 钻杆公接头与母接头
3钻杆接头强度有限元分析钻杆接头结构设计采用 2D 轴对称单元模拟,轴对称单元能以较小的计算成本达到非常高的精度。这里采用轴对称单元进行二维有限元分析计算。
利用 ABAQUS 软件对所建立的有限元模型进行计算,得出在该受力工况下的应力图,如图 4~6 所示:
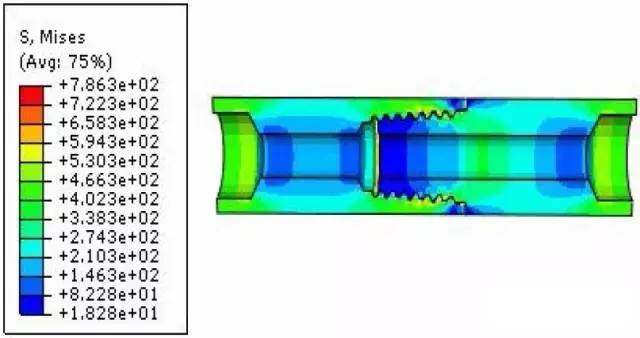
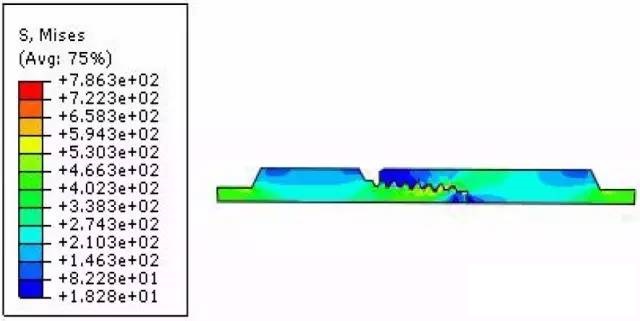
图4 钻杆接头等效应力
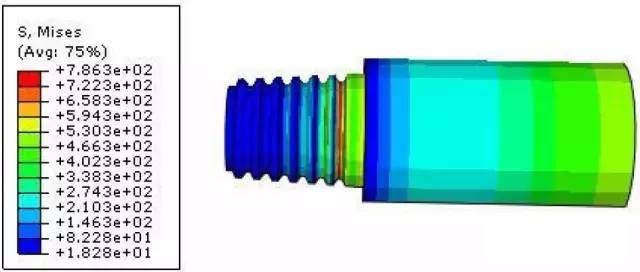
图5 钻杆公接头等效应力
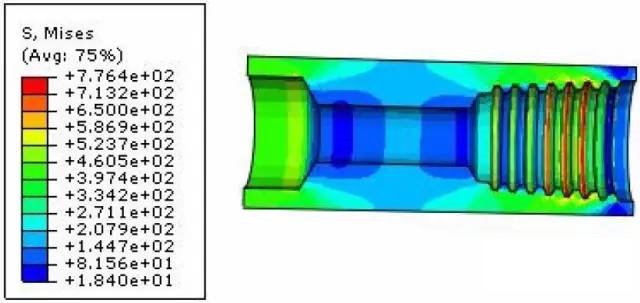
图6 钻杆母接头等效应力
从图可以看出其最大等效应力为 786.3MPa,分布在公、母螺纹的第一牙处。,就钻杆接头部分强度分析计算而言,钻杆接头螺纹处(第一螺纹处)应力值偏大。如果钻杆选用 45号钢,钻杆接头螺纹强度明显不足;如果钻杆选用 40Cr,钻杆接头螺纹强度基本持平;如果钻杆选用 42CrMo,钻杆接头螺纹强度富余量也不明显。
根据上述分析可以看出,钻杆接头螺纹应力值偏高,接头螺纹强度偏低,是导致钻杆接头断裂的原因之一。
4钻杆材质分析
钻杆的断裂现象始终是与材料和结构的孔洞、缺口或裂纹相联系的。在材料的这种宏观不连续部分最明显的特点是应力分布不均匀,这种现象称为应力集中。缺陷(孔洞、缺口、裂纹等)和应力集中往往是造成结构破损的最重要原因。从抽象的观点讲,缺陷的出现,导致完整材料的某些对称性破缺,而且导致数学上的奇异性发生,值得一提的是,出现在钻杆上的裂纹通常是横向分布的,并且靠近“加厚过度带”早期出现的裂纹大都在锥型体与管柱之间过度区域的圆周上,这个过渡区强度很高,这些裂纹通常直而无分支,自然形成穿晶现象,而且这些现象总是伴随着疲劳断裂。
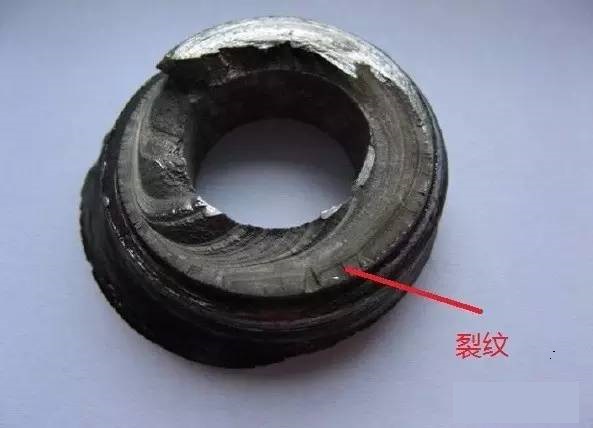
图7 断口宏观形貌
宏观形貌:肉眼观察发现,三次断口均有显著的旋转疲劳特征,第三次样件尤为明显。可见,裂纹起源于左上部位,在旋转载荷下沿逆时针方向疲劳扩展,断裂面积达到大约一半时(图 7 中直线处),弯曲应力的作用开始占据主导作用,疲劳纹大致与钻杆圆周平行。
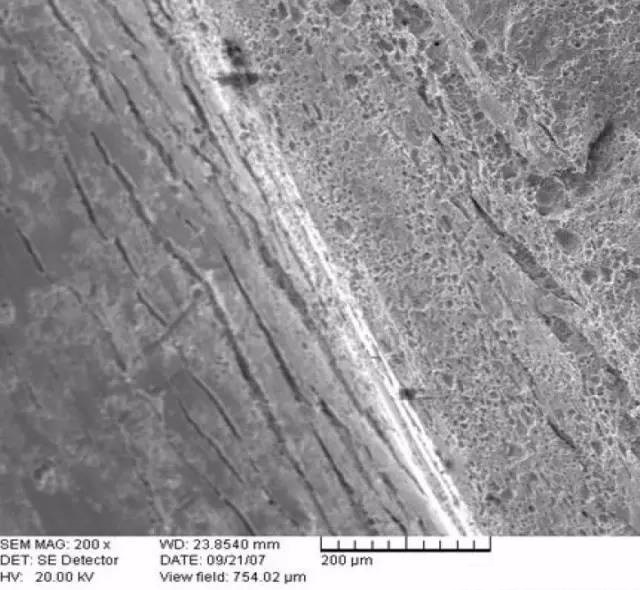
图8 裂纹

图9 腐蚀坑
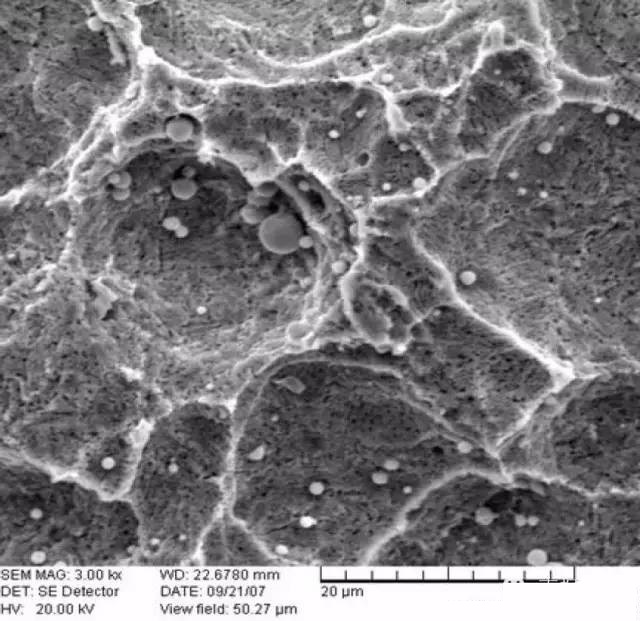
图10 韧窝
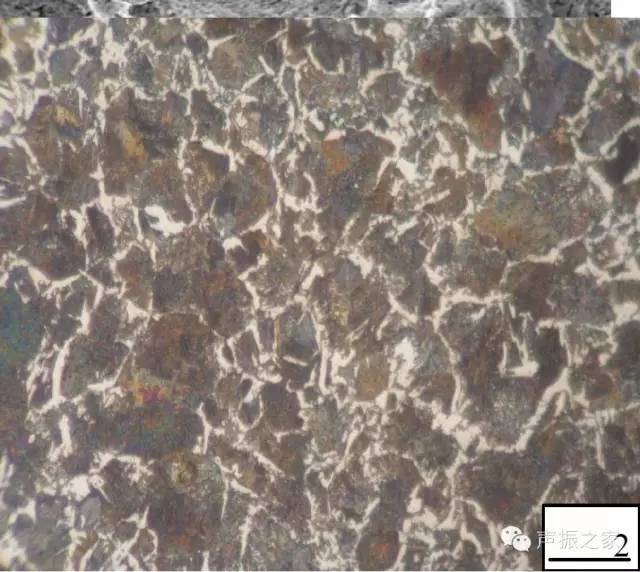
图11 珠光体+铁素体
微观形貌:利用扫描电镜观察了断口的微观形貌。发现断口靠螺纹根部的边缘较为平坦,与此处的应力集中有关,螺纹面有大量腐蚀坑和小裂纹,说明腐蚀对裂纹的产生有一定促进作用;断口微观形貌以韧窝为主,显示韧性断裂特征;珠光体较多,是其硬度较高的原因之一。
5失效原因分析及改进措施
5.1 失效原因分析
通过对钻杆螺纹进行强度分析和材质分析,找出钻杆螺纹失效原因:
① 应力集中:钻杆接头螺纹原始模型有限元分析结果表明:在公扣第一螺纹牙处根部受到严重的应力集中,极容易引起疲劳破坏。
② 热处理工艺不稳定:通过钻杆的材质分析可以知道:钻杆过渡段形成一个组织不稳定的高应力区。如果在组织不稳定区的表面存在缺陷,它可能来自热处理中裂纹,也可能喷砂不均匀,成为疲劳源区。由于高应力的作用,接着在外部循环载荷的作用下,裂纹疲劳扩展,钻杆发生过载断裂。
③ 存在腐蚀:从分析的样品看,外表面发生了严重的腐蚀点坑,当蚀坑的深度使管子的壁厚承受不了内部压力时,穿孔现象就会发生。钻杆的腐蚀属于煤矿井下酸性环境引起的腐蚀。与断裂不同,腐蚀是一个缓慢的过程,蚀坑必然存在一个积累过程。防止腐蚀失效的措施,首先是钻杆存放位置尽量远离井下酸性环境的来源,其次是定期的清洗是可以避免腐蚀失效的。
5.2 改进措施
1) 结构改进措施:针对导致钻头断裂的原因,考虑改进方案与原设计的互换性问题,从以下两个方面进行改进:
切削公螺纹大端第一牙,使螺牙承受载荷均匀化;
开弯曲应力减荷槽,避免弯曲应力出现在螺纹薄弱区域;
改进前后结构对比见图12,按照上述方法重新对钻杆接头的强度进行有限元分析计算,计算结果见图13-15。
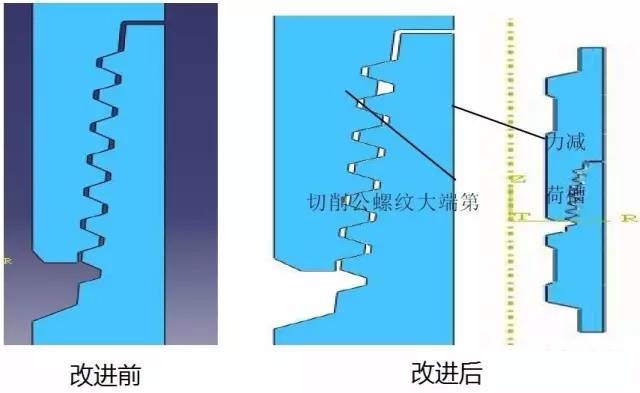
图12 改进前后结构对比分析
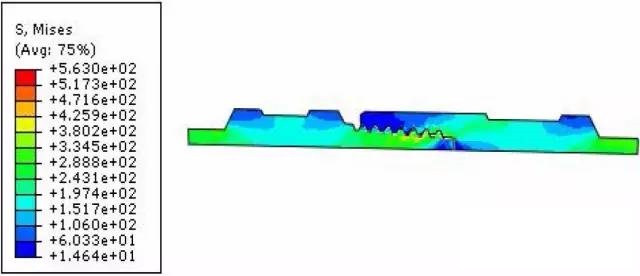
图13 钻杆接头等效应力
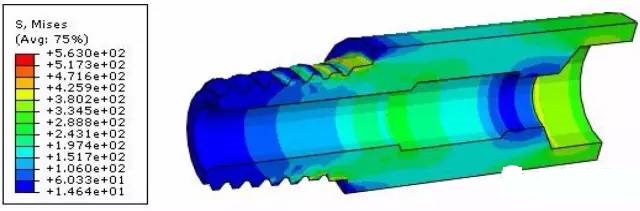
图14 钻杆公接头等效应力
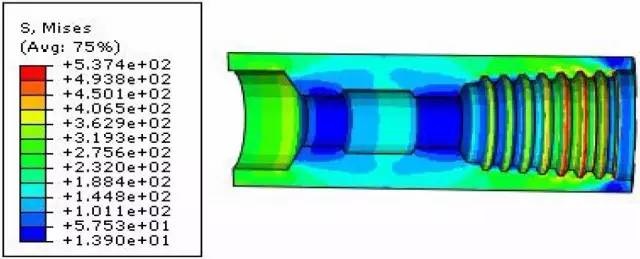
图15 钻杆母接头等效应力
表1 原始与改进方案结果对比表
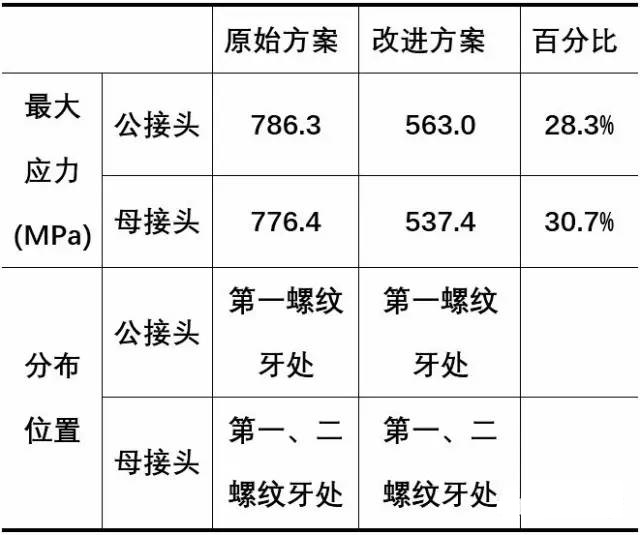
2) 材质及热处理改进措施:钻杆材料尽量选用强度较高的合金结构钢。严格控制热处理工艺和适当提高热处理后的硬度和强度,保证钻杆产品组织性能的均匀性和一致性。
6结论
通过上述改进措施加工出的钻杆,在全国多家大煤矿井下的实际应用,钻杆断裂的事故率明显降低,取得了较好的效果,为企业节约了大量的改进费用,缩短了改进时间,创造了较大的经济效益和社会效益。