新能源动力电池包热仿真
2023-5-21 17:42:50
详细介绍
01 电池包设计
电池组由多个相同的电池,BMS电流收集器,电池支架,冷却板,接线盒,和顶部和底部电池盖组成。所述单元可以配置为串联、并联或两者混合以输送所需电压和容量。仿真模型如图2所示。
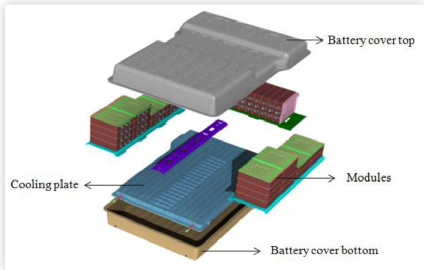
图2 电池模型拆解图
袋状电池由薄铝箔制成并包裹在聚合物层中;电池模块由多个袋状电池堆叠成外壳;热冷却泡沫垫沿外壳粘贴确保结构的稳定和散热;添加塑料框架保证标签分离防止短路。电池管理系统由微处理器和塑料芯片组成;NVH泡沫被用作结构构件抑制来自包装的噪声和振动。电池冷却系统在给定泵送功率下优化冷却流路,并按要求维持电池温度。母线和其他载流元件通常由铝制成,由于铝具有优良的导电性。ABS,丙烯酸和塑料用于连接器和各种组件的覆盖物。表3解释电池组的电池规格。表3 电池参数
02 CFD流程
图3介绍了含冷却系统和无冷却系统的电池热仿真的工作流程。
图3 流程图
03 CFD设计
图4建立了电池热行为的几何模型,电池组件及其材料性能如表4所示。
图4 几何模型
表4 电池材料参数
04 冷却通道设计
冷却通道的计算如下式所示:
其中,A表示冷却通道的面积(m2);M表示冷却剂质量流量(kg/s);V表示冷却剂速度(m/s);ρ表示冷却剂密度(kg/m3)。
05 网格
采用STAR-CCM+网格划分生成多面体网格,对于流体域,首先进行网格细化同时确定冷却管壁上的边界层。固体域的基础尺寸为5mm,流体域的基础尺寸为4mm。基于y+目标值1,体积增长率设置为1.2,边界层厚度设置为0.5 mm。此外,进行网格无关性验证,三种网格数量分别增加了25%,确定网格数量为1000万个。体网格如图5所示。
图5 网格模型
06 物理连续体
物理连续体是一个由数值定律和模型控制的环境,这些定律和模型将应用于我们模型的一个或几个领域。可以是气体、流体或固体,为每个固体和流体组件设置了物理。流体域采用隔离绝热K-Epsilon湍流壁函数模型,外固体表面考虑对流。与环境换热系数为10W/m2·K,固体部分的环境温度为300K。系统的边界条件为冷却剂进口质量流量352kg/h和温度24℃。收敛系数满足质量流量、温度和压力等所有因素。表5描述了连续体设置。
表5 CFD物理连续体
DOE矩阵 -热模拟
表6表示11种不同模拟的DOE矩阵,一种模拟是没有冷却系统,四种模拟是有液冷(2个进气口和2个出口),最后一类是有冷却(1个进气口和1个出口)。对电池系统进行了三种不同类别的模拟。
表6 DOE矩阵
07 无冷却系统的电池模型
图6为无冷却系统的CAD模型。在不考虑冷却剂流动的情况下进行了模拟,外罩对流速率为10w/m2·k,环境温度为27℃。
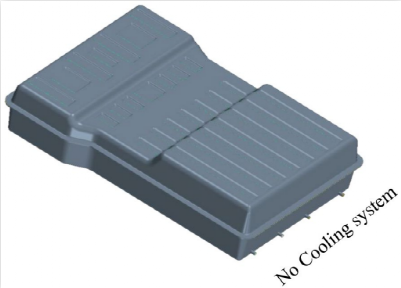
图6 无冷却系统的CAD模型
没有热管理系统的电池系统的结果,图7表示无冷却系统的温度分布;图8是截面温度分布;图9是图7为电池各部件的温度曲线图。可以看到内部部件的温度值超过了100℃;图10是各部件的最大温度图。
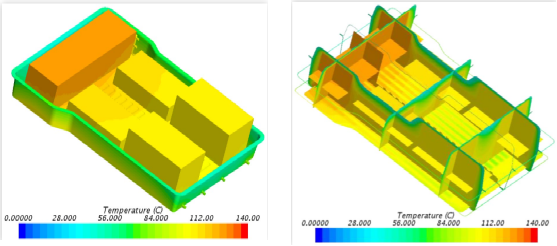
图7 温度分布 图8 界面温度分布
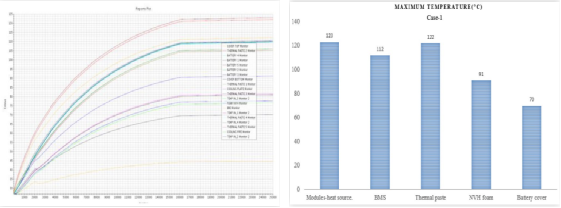
图9 电池各部件的温度曲线 图10 各部件的最大温度
电池系统在高温下的影响,如图11所示。
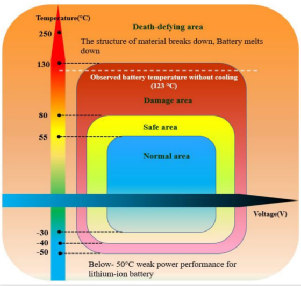
图11 无冷却系统的温度影响
08 带冷却系统的电池-第一类结构图12为第一类冷却结构系统图,有两个冷却入口和两个冷却出口。
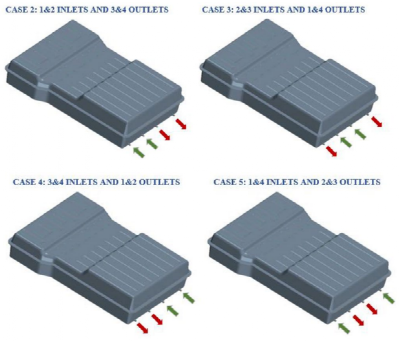
图12 第一类仿真结构
对冷却剂和固体分别设置各自的热特性和固体组分。电池使用的材料是铝、铝合金、热塑性塑料、导热润滑脂、NVH泡沫和40%乙二醇溶液作为冷却剂。对系统进行仿真分析结果如图13所示。case2(管道1&2进口和管道3&4出口)的温度均匀性优于其他情况,case 2中各部件的最高温度较低,主要是冷却剂带走了更多的热量。case2的压降为48.1mbar,这是由于通过冷却系统的流道造成的。
图13 温度分布
09 带冷却系统的电池-第二类结构
图14为第二类冷却配置的仿真结构图,包含一个进口一个出口。
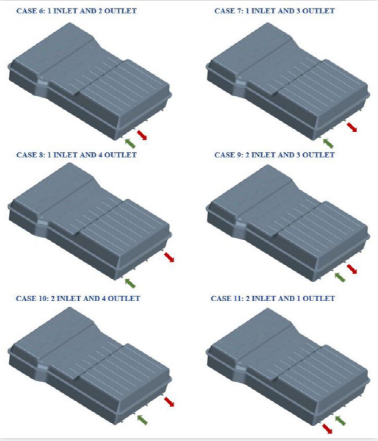
图14 第二类仿真结构图
从图中可以看出,case 8(1号管道入口和4号管道出口)的温度均匀性较好。由于电池系统的冷却剂传递了更多的能量,外壳8的电池部件温度最低
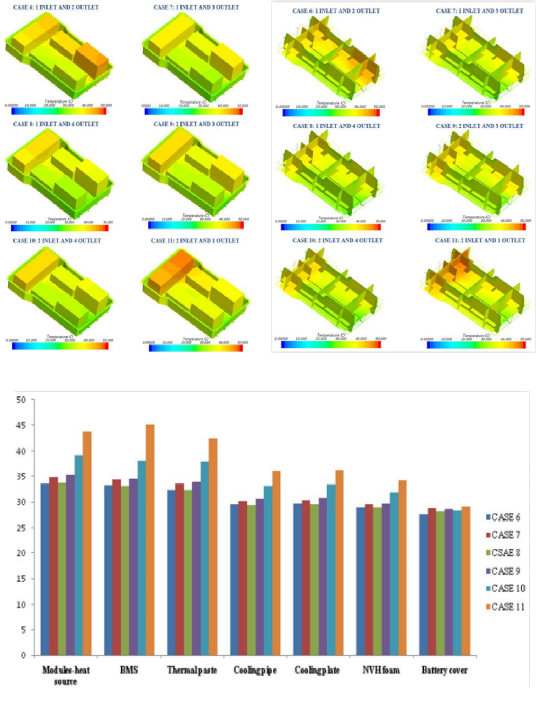
图15 温度分布
图16 冷却剂温度分布
10 总结
对不同电池配置进行了设计和三维仿真。没有冷却系统的电池系统导致其部件温度较高(高于120℃),从而导致系统故障。I型和II型冷却系统配置在最佳电池温度范围内运行(25-55℃)。I型(多进出水口)比II型(单进出水口)配置更好、更高效。考虑到电池的产热和温度均匀性,从冷却矩阵中选择case2(1&2个入口,3&4个出口)作为最佳配置。case2的压降为48.1mbar,电池部件中最低温度(34.55℃)。
结果和讨论
为了实现电动汽车电池包的冷却性能和成本效益,热管理和冷却系统类型的选择是非常重要的。电池系统的冷却涉及到冷却方式、冷却系统的设计、电池冷却系统的进、出口等几个因素。在本文中,电池热管理系统选择了液冷方式。没有选择风冷方式,因为风冷系统的传热系数比液冷要低,且空气的热容量小,很难保持包内的温度均匀。选择40/60比例的水和乙二醇混合物用于间接冷却系统,因为它在车辆应用中具有较低的冻结温度。水/乙二醇具有较高的热容量,因此采用水/乙二醇作为传热流体可以大大减小系统内部冷却液的温度变化,同时也可以达到温度均匀性。